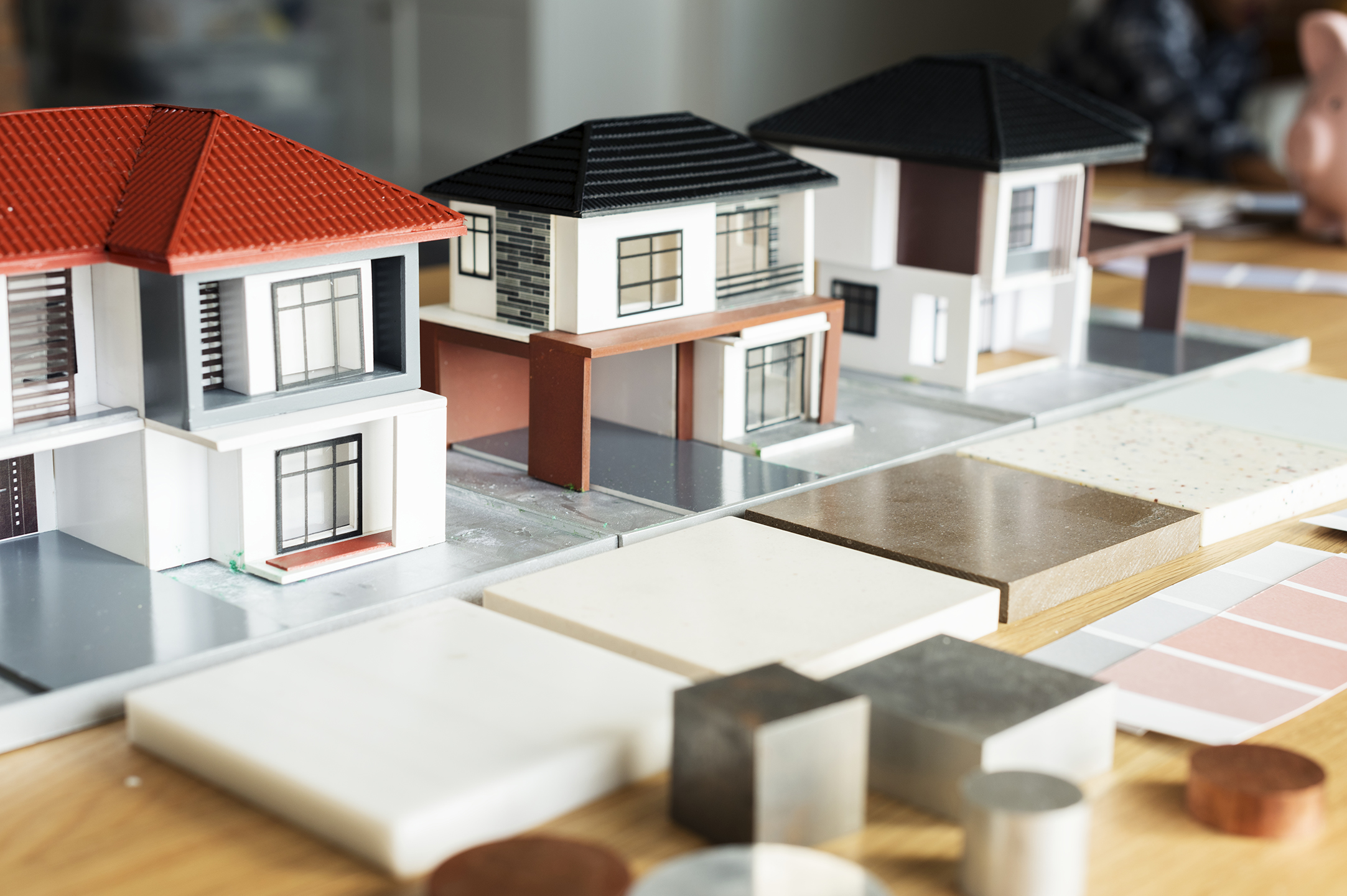
Incentives for Developing Multifamily Affordable Housing
February 24, 2020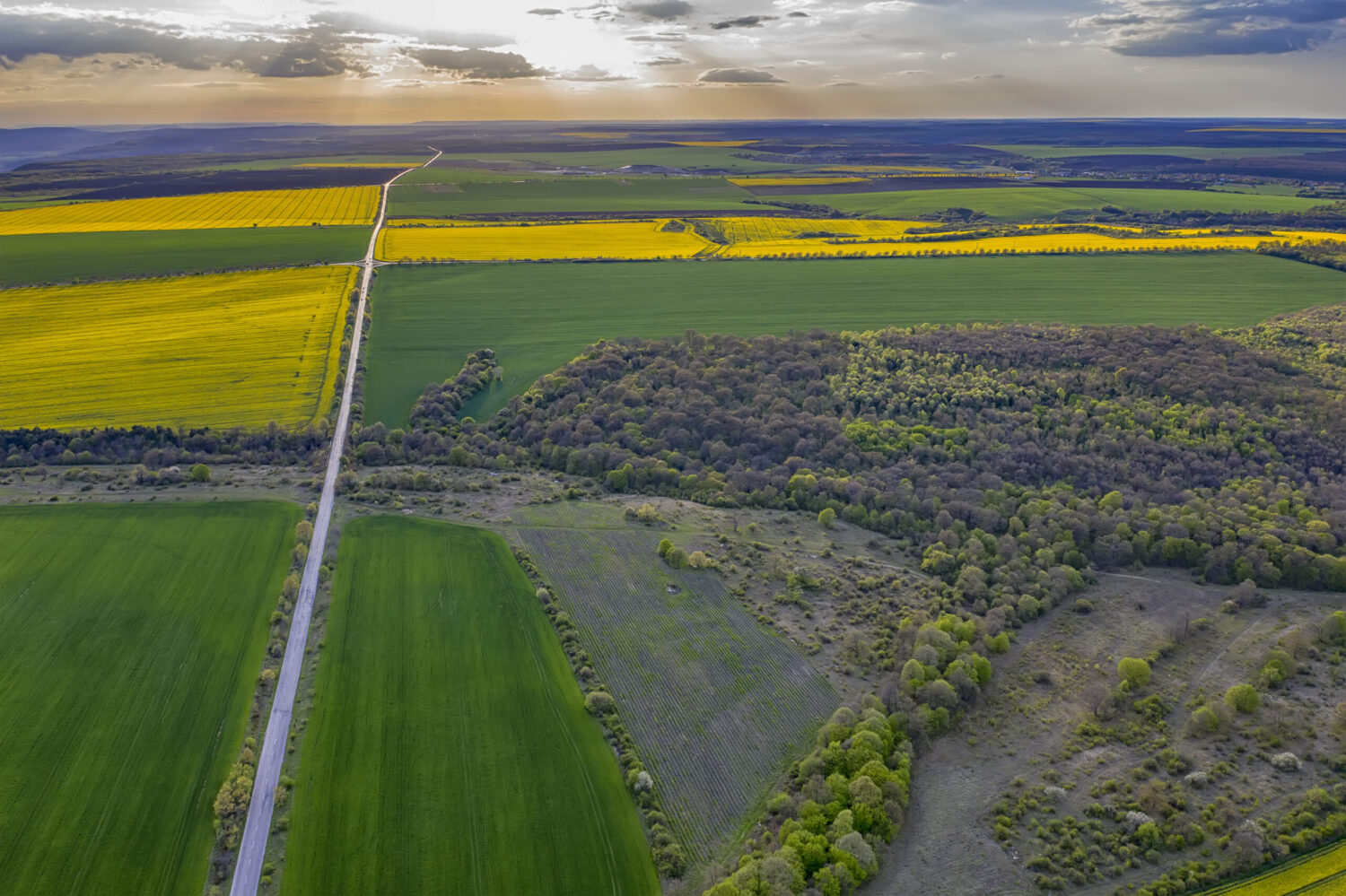
Engaging a Development Adviser for your Master Plan
June 2, 2020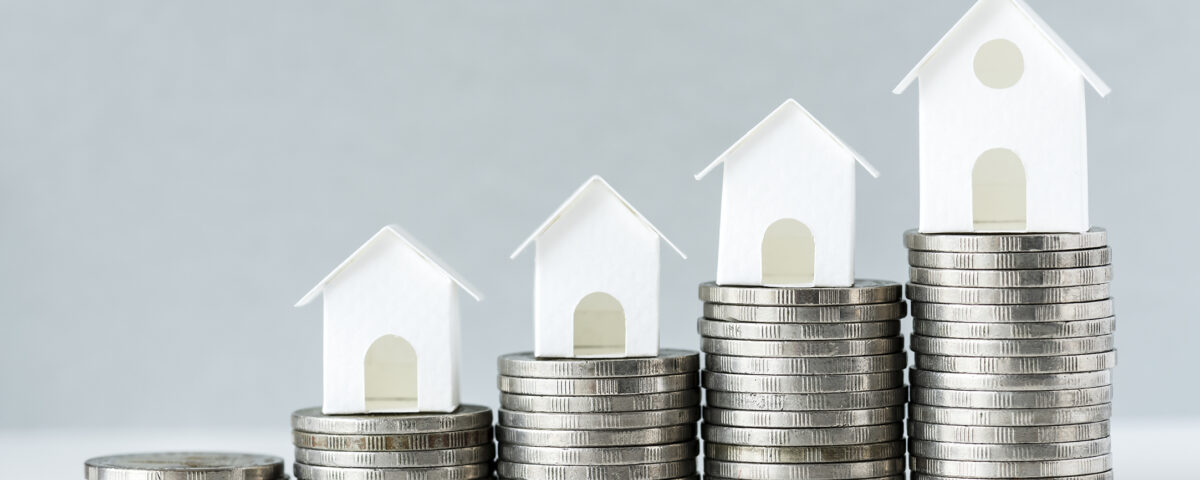
Innovative Construction Methods Help Developers See a Faster Return on Their Investment
The construction industry is changing, and shortages of skilled labor in the field can impede a project’s development schedule and impact the bottom line. But knowledgeable and resourceful architects are designing in some innovative construction methods that are helping projects complete on-time and with a higher quality, all while adhering to the budget.
There are three methods architects are employing to remove variables and inconsistencies in commercial real estate construction:
• Panelization are cold formed steel components or wall assemblies manufactured in a factory and shipped to the construction site for easy erection. The architect’s design is sent to a manufacturer who creates wall assemblies from the plans that are ultimately of higher quality than site or stick built construction.
• Proprietary grid-based kits are manufactured and assembled – often using robotics – in a factory, then shipped to the construction site for quick erection. This method can be somewhat limiting to design, as the grid is typically a predetermined grid module.
• Modular rooms are completely fabricated in a factory and shipped as an all-inclusive unit to the construction site, where they are hoisted into place. The only limitation is the ability to transport the module to the site.
One of the unintended benefits of utilizing one of these methods is the quality assurance that comes with the finished product. Factory and robotics-produced repetitive manufactured components are far more consistent than the common “rule of thumb” often used in the field. Every piece fits seamlessly with another, as the designer intended, creating a far superior building, and the assembly time is shortened considerably. Additionally, in dense urban areas where staging and lay-down space is limited, the ability to manufacture panels and components offsite and precisely schedule their delivery for immediate installation onsite ensures a more efficient process.
A more consistent product and faster assembly on site ensures the project adheres to the schedule, stays on budget, and is ultimately of higher quality. This process helps the property owner occupy the building and start seeing revenue sooner, often up to 2 months. To put that into perspective, for example, to a one hundred unit assisted living community, it can mean $200,000 or more that the owner sees for each month the building is occupied ahead of schedule.
While the product itself may be slightly more expensive than its wood counterpart, the guaranteed savings in construction time and skilled labor with a higher quality building are of significant value for a developer. The integration of the design team, including a development adviser with knowledge of these methods who can bring the experts to the table, ensures the team is working together to innovate and find new ways to do things on behalf of the property owner. Ensuring developers and owners see a faster return on their investment is valuable for everyone involved.